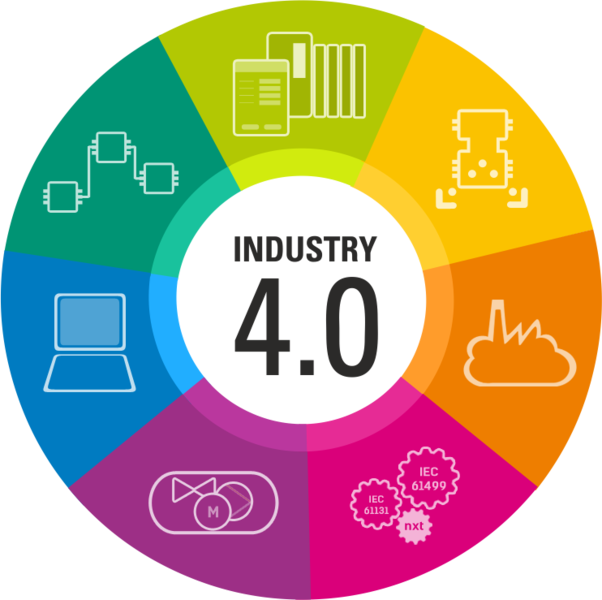
Industry 4.0 is the name for the increasing combination of traditional manufacturing and industrial platform practices with the latest smart technologies, with an emphasis on the use of large-scale M2M and Internet of Things (IoT) applications to provide, for example, greater automation, improved communication and monitoring, and intelligent machines that can analyze and diagnose problems without human intervention. The recent evolution of big data analytics platforms means that systems can sift through vast data sets to gain insights that can be reacted to quickly and efficiently. It uses the Internet of Things and cyberphysical systems, such as sensors, to collect huge amounts of data that can be used by manufacturers to analyze and improve their work.
Industry 4.0 is the current trend in the fields of automation, data exchange and manufacturing technology. Automation plays a significant role in typical components of cyberphysical systems and the Internet of Things where quality aspects of robots can be monitored in real time to reduce errors. By linking your production system and its wider environment with sensors, software, IoT technologies and systems to gain insight from customers, you can improve the quality of your products.
Industry 4.0 is revolutionizing the way companies manufacture, improve and distribute their products. Manufacturers integrate AI-enabled technologies such as IoT, cloud computing, analytics, AI and machine learning into their production and operations. In this new era, manufacturing processes are faster and more efficient than in the past by analyzing vast quantities of production data and using machine learning and artificial intelligence.
We are in the midst of a significant change in the way we produce products, thanks to the digitization of manufacturing. This transformation is so compelling that it is called Industry 4.0 and represents the fourth revolution in manufacturing. While the first industrial revolution was the mechanization of water and steam to power mass production and assembly lines with electricity, the second and fourth revolutions began with the third: the introduction of computer automation, reinforced by IT, intelligent and autonomous systems powered by data and machine learning.
The Fourth Industrial Revolution is essentially a trend of automation and data exchange in manufacturing technologies and processes, including cyberphysical systems (CPS), IoT (industrial Internet of Things), cloud computing, cognitive computing and artificial intelligence. It promotes what is called a smart factory. Instead of dismissing the fourth revolution that has taken place in manufacturing as a marketing slogan, the transformation that is taking place in manufacturing deserves our attention.
Industry 4.0 is based on the Industrial Internet of Things (IIoT), cyberphysical systems and intelligent autonomous systems that use computer-aided algorithms to monitor and control physical things such as machines, robots and vehicles. Cyberphysical systems monitor physical processes in modular and structured smart factories, create a virtual copy of the physical world and make decentralized decisions in virtual buildings. Industry 4.1 will make your supply chain smarter, from smart manufacturing factories to smart warehousing and logistics.
Industry 4.0 is a series of technological changes that have created a coherent framework for introduction into the production process. The backbone of the industry relates to product manufacturing phenomena that affect all parts of the world and affect all types of companies. The simplified definition of Industry 4.00 is the use of IoT, cloud computing, cyberphysical systems (CPS) and cognitive computing in the manufacturing and service environment.
Digital technologies create virtual versions of real installation processes and applications. These virtual systems can be tested by decentralized decisions and designed cost-effectively. Physical Digital takes physical actions and converts them into digital recordings, and Digital shares insights with the help of AI, which has been part of manufacturing for years.
Large-scale machine-to-machine communication ( M2M ) and Internet of Things ( IoT ) will be integrated to increase automation, improve communication, monitor production itself and deploy intelligent machines to analyze and diagnose problems without human intervention. Industry 4.0 will lead to massive increases in productivity and efficiency, enabling you to offer better services to your customers. The term refers to the world of the Fourth Industrial Revolution in which technology connects people, systems and digital ecosystems where data are collected, used and optimized for operation in real time.
Industry 4.0 refers to a new phase of the industrial revolution that focuses on networking, automation, machine learning and real-time data. It includes IIoT and smart manufacturing, which combine physical production with smart digital technologies such as machine learning and big data to create a holistic connected ecosystem for business focused on manufacturing and supply chain management. Industry 4.1 is defined as the name of the current trend in automation and data exchange in manufacturing technologies, including virtual and physical systems, Internet of Things, Cloud Computing and cognitive computing to create smart factories.
It describes the rise of automated systems and data exchange technologies in the manufacturing industry. Industry 4.0 is a concept associated with the Fourth Industrial Revolution (4IR) and is associated with the further development of cyber-physical systems. This type of automation occurs when manufacturing systems, devices and technologies used in production are connected using sensors to monitor and visualize the entire process.
During the Third Industrial Revolution, manufacturers underwent a transformation that relied less on analog mechanical technology and more on digital technology, automation, and software. The invention of technologies such as transistors and integrated circuits revolutionized manufacturing by automating machinery in the factory floor, resulting in less effort, higher speed and greater accuracy, while freeing human labor for more advanced tasks. In recent decades, a fourth industrial revolution has developed, known as Industry 4.0.
The third industrial revolution was called the Digital Revolution because of the rapid adoption of digital electronics. Microprocessors, PCs, mobile phones, and the Internet were the most important technologies of that era. The concept of Industry 4.0 was introduced in the 1990s, when the Internet and telecommunications changed the way we connect and exchange information.
Building on the Third Industrial Revolution which led to the creation of personal computer and the internet, Industry 4.0 takes technology into the next evolution, blurring the boundaries between the digital and the physical worlds. Elements such as automation, IoT and more are becoming more widespread than ever. It is also known as the Fourth Industrial Revolution (4IR), an all-encompassing term that refers to the way computer systems, data and automation evolve and come together to change the way we work, particularly in manufacturing.