Welcome to the world of Ethernet/IP. When setting up an Ethernet/IP-based PLC, you may be wondering why you must configure some devices and not others. The answer lies in the differences between “connected” and “unconnected” configuration for Ethernet/IP.
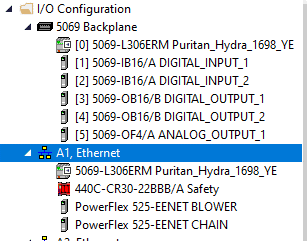
Connected vs Unconnected, Explicit vs Implicit, Scanner vs Adapter. These are just some of the acronyms you need to know if you plan on becoming a networking pro!
CIP is a communication protocol that’s used by many popular communication protocols in the industrial automation sector. It encompasses protocols such as CompoNet, EtherNet/IP, DeviceNet and ControlNet.
What makes CIP unique are (something you can honestly not care about)
- Producer-Consumer Architecture
- Managed jointly by ODVA and ControlNet International
- Object-Oriented Approach
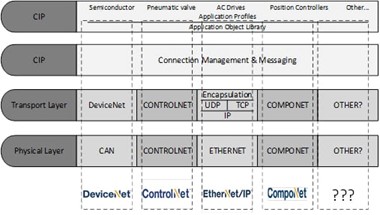
This brings us to EtherNet/IP, the most widely used protocol in today’s automation. EtherNet/IP became the most popular protocols for many reasons. For typical reason, it combines the most popular Ethernet with CIP, and can coexist with existing network. This allows EtherNet/IP to take advantage of the existing Ethernet infrastructures and gain huge popularity recently over other CIP based protocol. The second main reason (skip to next paragraph) is the push by AB to make it the most domain protocol. AB is the most domain player in the industrial automation market, and when AB PLC only speaks EtherNet/IP, you must adapt EtherNet/IP onto your hardware/software or be left out.
Anyway, in a EtherNet/IP network, each device has to have a unique IP address. Additionally, in a EtherNet/IP network, there has to be a master, and the rest are called slaves. A master can have as many slaves as possible, but a slave can only have one master. Some people refer to Master as Scanner, and Slave as Adapter. In short, when you heard Master in the domain of EtherNet/IP, think of Scanner that is constantly looking for slaves, or adapter.
Once the slaves and master are determined, we will than discuss on ways of communicating between slaves and master.
Think about it this way: if all data is communicated as fast as possible, there won’t be enough computation resources left to scan the PLC ladder logic. It’s important to have a balance between speed and resource allocation.
Modules like PowerFlex are implicit messaging because they contain all the information you need to know, without the need for critical information. HMI modules, on the other hand, communicate critical information that is not time-sensitive.
Explicit messaging communicates the message without any interference, while implicit messaging is always connected to the master and slave. When you disconnect a HMI to the PLC, there is no error on the PLC. However, if you were to disconnect a ‘connected’ device to the PLC, the PLC will indicate an error in the modules section.
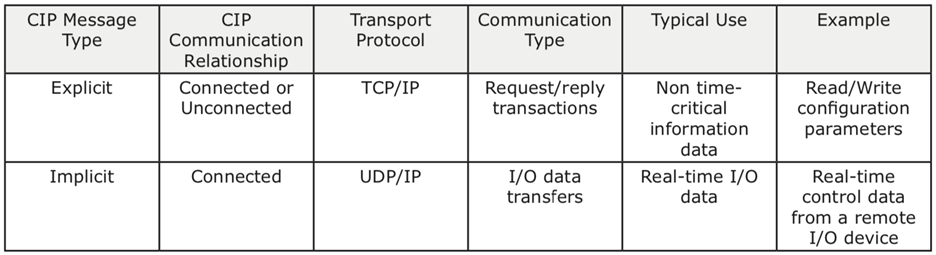
The main take away are the following:
- There can be only one master, and as many slaves as you wish (depending on the available IP Address)
- A master is usually the decision maker, which is mainly the PLC.
- Not all devices can be a master.
- Just because you have a bunch of EtherNet/IP devices, do not mean they can talk to each other. Most of the time you are born into either a master and a slave, and very few devices can do both.
- Use Explicit messaging for noncritical data and Implicit messaging for critical data.
- Too many implicit data will slow down everything.
- IP in EtherNet/IP dose not stand for Internet Protocol, but Industrial Protocol.
- But honestly who cares…