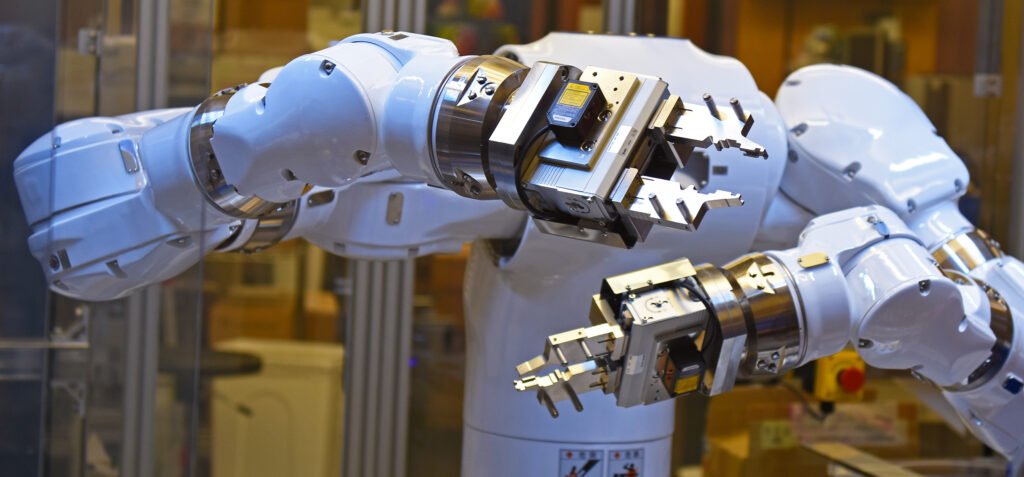
Inventor George Devol filed a patent in 1954 for the first industrial robot, and when it was brought to life in 1961, it looked and functioned much like today’s robotic arms capable of carrying 500 pounds and performing tasks previously reserved exclusively for humans. Robot arms are now a familiar sight in automobile factories and other production facilities.
Robotic automation can be used in industries of many types and sizes of manufacturing companies. Robots can perform tasks such as welding, assembly, shipping, handling raw materials and product packaging. More and more manufacturers are using robotics and automation for a variety of applications.
Autonomous manufacturing robots are needed for large-volume, repetitive processes in which the speed, accuracy, and longevity of robots offer unprecedented benefits. Manufacturing robots can automate repetitive tasks, reduce error margins to negligible rates and empower human workers to focus on more productive areas of work.
To reap the full benefits of advanced robotics, a company should assess the system architecture that supports its operations and processes to reap full benefits. It should establish a broad range of capabilities, including those relating to edge computing, analytics, data and workflow management, cybersecurity, industrial software, automation and device infrastructure. By training new employees and by employing external experts, companies can acquire essential knowledge on how to integrate advanced robots into operations best.
In food and beverage production, a large proportion of the factory workers are in the packaging sector. This could mean big savings if automation and robotics take on repetitive tasks and are integrated into the factory floor. Robots could, for example, replace skilled workers who work with gems or assemble small electronic devices.
Early robots followed the same path as later iterations, using laser vision systems to determine the orientation of parts and materials, but the latest generation of robots integrates information from multiple sensors and adjusts their movements in real time. Touch control and 3D visualization give robots freedom of movement, i.e. They are not bound to a task or place. For example, they can mimic the skills of craftsmen in grinding, deburring and polishing using force feedback.
Data analysis and automation, applied across the entire supply chain, can enable new plant production systems at any time in production. These new systems offer more flexibility and agility for plants to respond to fluctuations in demand and reduce waste and costs.
This has led some companies to use automation technologies to replace old assembly lines and gain access to new production models with this efficiency. Companies like Tesla have embraced the concept of super-automated factories, which means heavy investment in robotics. Although this concept is sound from a business point of view, the necessary technology has not succeeded in surpassing the automation models of companies such as Toyota.
Motivated by the need to produce parts for less, manufacturers of all sizes rely on various forms of automation to reduce costs, increase production and shorten response times. Automation is changing the face of manufacturing in a way never imagined before – from large production plants with robots to small job centers that want to improve a few important production processes.
These conditions create opportunities both for manufacturers of automation technology and for plant engineers at home and abroad. The latter creates opportunities for automation manufacturers and plant engineers alike.
Decisions about advanced robotics go beyond capital investment and include strategic decisions that affect many aspects of an industrial enterprise’s business model, such as product mix and manufacturing area. To grasp the full extent of these decisions, companies need to develop a holistic, targeted picture of the factory of the future. This includes the implementation of several automation technologies, including advanced robotics.
In today’s manufacturing, simple, repetitive tasks can be automated using robots without massive infrastructure investment to avoid variability. Robots are used in e-commerce warehouses to automate material transport and sorting processes. The holy grail of manufacturing is achieved with hyper-automated factories where all manual activities in the manufacture of robots are carried out.
Thanks to recent advances, modern robots can be programmed to perform new tasks. Robots can be used for high production in high-volume environments and scaled for use in fast-growing companies. However, robots in cells today require adaptations in order to be able to work with certain products and processes, which requires time, resources and costs.
Advances in artificial intelligence and sensor technology allow robots to manage a greater degree of variability from task to task. The ability to adapt their actions to changes in their environment creates opportunities for automation in areas such as agricultural processing where a significant part or part of the variability (e.g.
To date, most robots have been used in manufacturing, where they perform a variety of manual tasks for humans. There is no specific hard and fast definition of robotics, but generally it refers to physical machines programmed to perform a variety of different tasks at each level of interaction with the environment with limited operator involvement.
The term “automation” was coined in 1945 when the Ford Motor Company design department used it to describe the operation of its new transfer machine that loaded dies from a press and put them in front of a machine tool. Today, the term refers to production processes that can be controlled by machines with low operator input in order to produce automatically. There are many technologies that enable the automation of production processes, and robotics is an important one.
One of the largest robot manufacturers in the world is the Japanese firm Fanuc (Fuji Automatic Numerical Control), which introduced automated factories in the early 2000s. Fanuc developed a platform to customize industrial robots using software applications. Now Fanuc is on the verge of becoming like Alphabet or Apple, earning revenue from software developers developing apps for industrial robots.
Their platform will set a common standard for application development and integrate a variety of robotic systems including those based on big data and artificial intelligence, which will facilitate the creation of automated factories of the future.