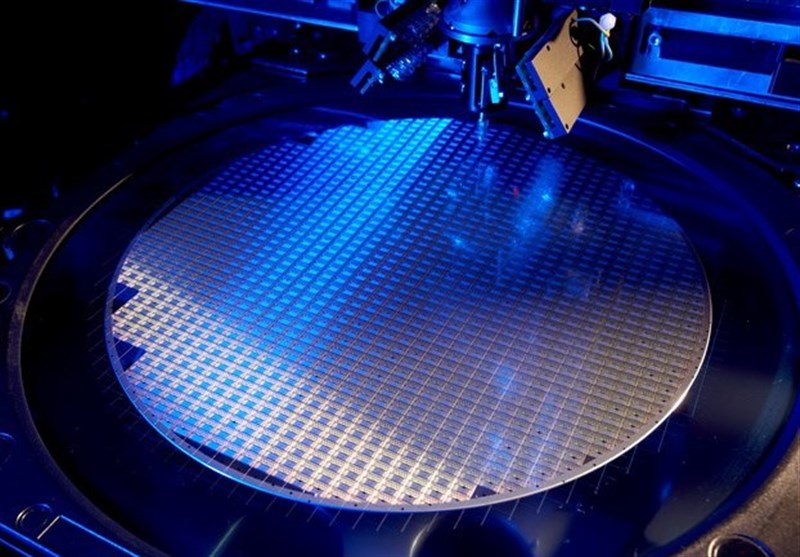
Ford Motor Co. said in a conference call on April 28 to announce first-quarter earnings that he is likely to lose half its production in the second quarter due to chip shortages. General Motors expects chip shortages to cut its profit by $1.5 billion to $2 billion this year.
The research firm IHS Markit expects to produce 672,000 fewer vehicles in the first quarter of 2021, including 250,000 units in the world’s largest auto market, China, due to a shortage of semiconductors. However, the company estimates that demand for semiconductors will grow faster than expected in the final quarter of 2020. There are no signs that semiconductor suppliers will be able to absorb this demand, based on forecasts for light vehicle production during 2021, especially in the second half of the year.
Automakers around the world are expected to lose billions of dollars in revenue this year because of a shortage of semiconductor chips – a situation that will likely get worse as the companies battle to supply critical parts. Consulting firm AlixPartners expects the shortfall to reduce global automotive industry revenues by $60.6 billion this year.
This is a conservative estimate that covers the entire supply chain from dealers to automakers, from large Tier 1 suppliers to their smaller counterparts, said Dan Hearsch, managing director of New York-based Automotive and Industrial Practice.

Semiconductor bottlenecks hurt manufacturers of automobiles and other products and illustrate the need for companies to make their supply chains resilient. Besides shortages of semiconductor chips, supply chain problems make it difficult for some companies to keep up with production. Tech Data sees the global shortage as the need to create resilient and flexible technological supply chains.
Chips are an integral part of things like household appliances, computers and cars. The Wall Street Journal explains that the shortage of semiconductor chips is not limited to cars and electric vehicles. If businesses cannot keep up, it is likely to drag on into next year.
In an interview with the CBSs program 60 Minutes, Pat Gelsinger, Intel’s new CEO, said several companies are coping with the looming chip shortage. Chip shortages have become a major problem for manufacturers since the outbreak of the pandemic. So the chip bottleneck will persist and affect several companies, and for Gelsinger’s company it will not be resolved anytime soon.
Several companies are addressing the threat of chip shortages by using effective methods to increase the production efficiency of chips. Chip shortages are expected to continue in the coming months, but plans are being drawn up for the resilience of supply in research, development and manufacturing.
IBM has been helping to strengthen the US supply chain for microelectronics for years, and today’s challenges are no exception. We have begun to lay the foundations for an ecosystem that will help secure and drive the supply chain and cover the costs of the next generation of AI chips and system innovations domestically to meet future needs.

In addition to investing in manufacturing capacity in America, accelerating investments in advanced semiconductor research and development will drive next-generation innovation and maintain the US leadership in this critical technology. Financing the construction of new semiconductor factories will take at least five years.
The chip shortage is in large part a ticking time bomb that has been building since late last year, with a few intermittent supply chain disruptions. The COVID-19 Pandemic caused a sharp drop in vehicle sales in the spring of 2020 and automakers reduced their orders for parts and materials, including chips for functions ranging from touch-screen displays to collision-avoidance systems. In the third quarter, demand for passenger cars recovered, and the chipmakers committed to supply their largest customers – consumer electronics.
The automotive industry was so focused on lean manufacturing and optimizing the cost of the supply chain that automakers stopped buying semiconductors to get critical components where they were needed. Chip factories decided to focus on the electronics industry, which has seen unprecedented demand for consumer goods.
Kamak points out that it is easier for the semiconductor industry to supply a large number of devices to factories in the region than to provide parts to automotive factories all over the world, because the chip manufacturers are based in Asia. At the same time, American firms have been unable to source chips from Chinese-run factories, complicating supply constraints even further. Tensions between China and the US have recently risen again, and semiconductor supply chains are showing signs of strain as assembly lines are struggling to keep pace with demand.
In January, TSMC announced that it was prioritizing its manufacturing efforts to help the automotive industry address its woes. It pledged $100 billion to increase its chip production capacity over the next three years and asked global manufacturers to rethink their semiconductor procurement strategies.
The current chip shortage is disrupting the automotive business and value chain, as OEMs and their suppliers rush to source reliable chip sources. Automakers in India, especially those based there, seem to be waiting to overcome the chip famine by curtailing production while their global counterparts get creative to address the persistent shortage of semiconductor chips. The shortage has led Indian automakers and premium bicycle makers to curtail production in some categories.
As automakers contemplate their next steps and semiconductor manufacturers struggle to keep up with demand, industries need to adjust their short- and long-term strategies to best weather supply chains disruptions.
Automakers are suffering the pain of the global chip shortage, which is extending into its fifth month, with some companies forced to stop production of certain vehicles and others deprived of the ability to rely on chips at all. Automotive and industrial services provider AlixPartners estimates that production of 3.9 million vehicles will be lost in 2021 due to ongoing semiconductor shortages. The company said in a forecast that the shortfall will cost the global automotive industry $110 billion in lost revenue this year, more than 80% more than its estimate of $61 billion in late January.
The global semiconductor shortage, which began in the first quarter of 2021, has brought assembly lines around the world to a standstill due to long lead times for tiny silicon chips and slowed production of smartphones, household appliances and driver assistance systems. Major automakers, including U.S. OEMs, have announced significant production cuts, slashing expected revenue by billions of dollars in 2021.
Machine Vision Integrators