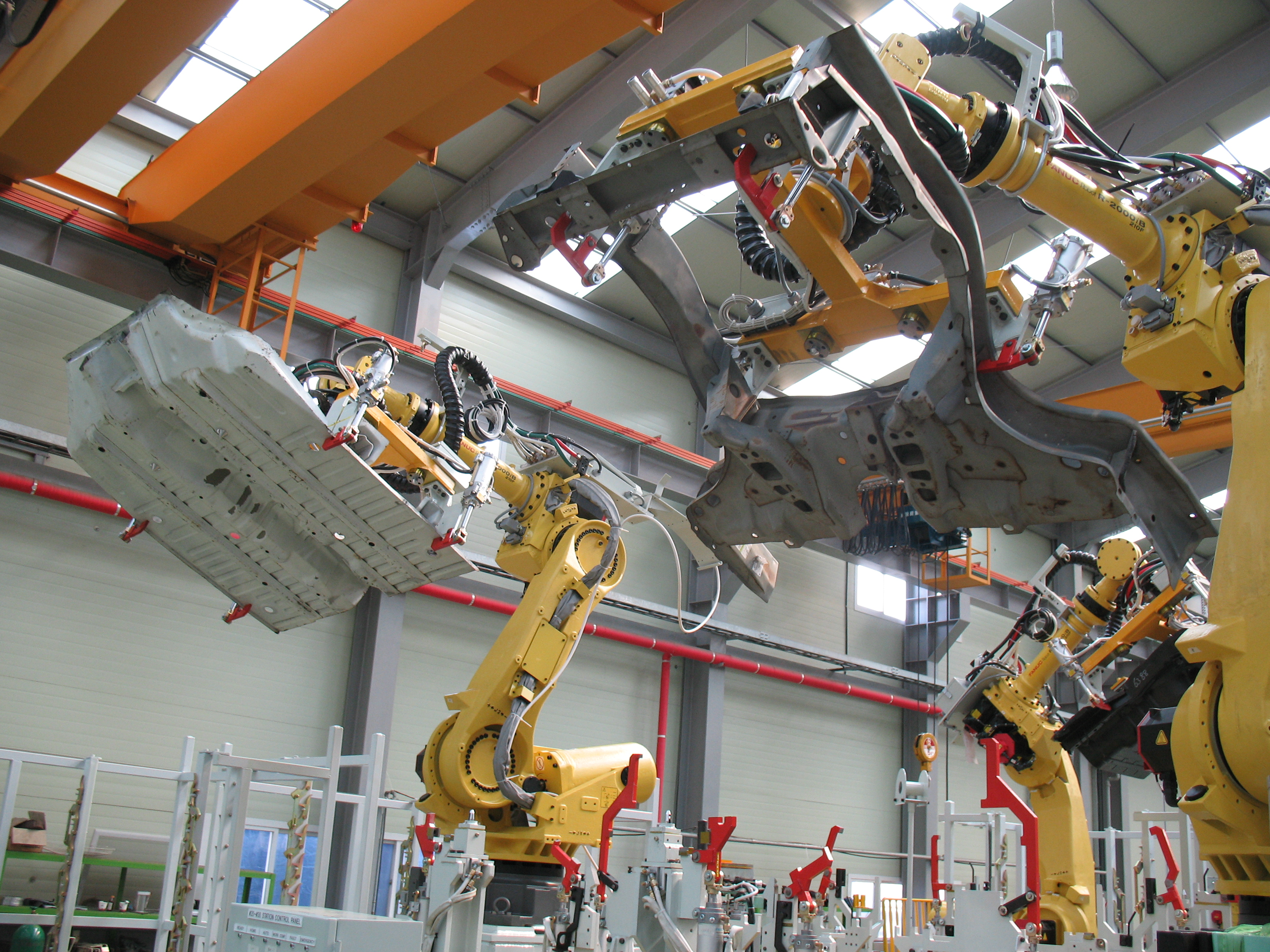
Modernization is a top priority for plant managers because it increases reliability and alleviates some of the safety concerns that older equipment brings with it. Equipment modernization enables companies to introduce modern technologies that support the cloud and IoT capabilities that are becoming more and more commonplace. Direct replacement solutions reduce downtime with minimal equipment and bus failures.
Investing in new equipment is investing in your business, without mention giving your team the tools to succeed. Buying new equipment can bring significant benefits, especially for small businesses. Appropriate investment in new plants enables higher quality products to be delivered and reduces waste.
Improving these assets will improve the efficiency of your business, reduce accidents and injuries, and help increase your customer base. The modernisation of industrial facilities is an investment in the future, but it is a challenge for most companies. One of the biggest obstacles to equipment modernisation is cost and time.
Before you decide whether or not to upgrade your equipment, you must make a thorough assessment of the condition and expected lifetime of your equipment. Upon completion, you can make an informed decision as to whether it makes more sense to upgrade a particular machine or the rest of the line. It is crucial that you evaluate devices with finished temperature sensors.
It can be difficult to detect the current condition of the equipment without costly inspections. By keeping detailed records of each component in your plant, you take into account how age affects the efficiency and safety of the equipment in question. By recording the condition of each part, changes in the environment, operation and service intervals, plant managers can improve visibility of plant conditions.
Most manufacturers cease part production if the device models are more than a decade old. Upgrades can help tight operating budgets by extending the life of existing plants. Improved equipment facilitates product assembly, increases working comfort and makes everything more durable and aesthetic.
As a result, it will be more difficult to obtain and buy spare parts as the equipment ages and needs maintenance. While repairs tend to be the cheapest option in the short term, replacement or upgrading may be warranted when safety issues or economic factors require it. Modern equipment has a greater availability of spare parts, making repairs and upgrades more affordable, workable and less time consuming.
Deciding what to do requires an accurate and complete cost-benefit analysis of several factors. They need to justify costs based on factors related to obsolescence and business objectives. The first two obstacles are the hardest to combat, but the third provides the ammunition (if you can put it that way) needed to achieve the business goal.
Your system needs to expand its capabilities by upgrading it with new features to meet your business goals. Don’t forget to consider the impact on your secondary systems such as network infrastructure and field equipment.
Modernisation of your production facilities is a significant investment in your manufacturing facilities to improve the performance of your plants and to keep up with the latest innovations resulting from the Industrial Internet of Things and other changes brought about in the industry. On the one hand, the modernisation represents significant investments, but remains a crucial part of the operation. Technological improvements will continue to be made to existing product lines and new capabilities will be introduced while your manufacturing facilities are installed.
In order to keep sub-costs low and maximise profitability, it is crucial to ensure that you have a strategy for equipment modernisation that includes implementing appropriate upgrades and replacing old and existing equipment with new equipment. There are ways to fix the deficiencies of the old factory equipment, but they do not have to go over budget.
Managing the operating costs of injection moulding equipment throughout its life cycle is critical to profitability. My company, Husky Injection Molding Systems, provides integrated services to help customers achieve lower total part costs throughout the product lifecycle. Chris is Managing Director of Factory Services at Husky.
The aim of the processors is to manufacture products at minimum cost without compromising the quality, functionality, reliability or delivery of the parts. Appropriate upgrades and the replacement of old equipment can reduce parts costs and improve the competitive profile.
Upgrading can be expensive, and there are many companies that do not realize the value of installing a new system. This is because only 30% of the new system capacity is used.
Once the benefits of new equipment are recognised and used, improving equipment becomes an advantage, not a pain point. By upgrading your equipment today, you can be better prepared for the demands of tomorrow’s major projects.
When it comes to the upgrading of devices and systems, rather than simply replacing them, it is important to note that IIoT offers exciting new possibilities for troubleshooting individual components and production lines. Based on state-of-the-art IoT-related solutions in predictive maintenance, data analysis, machine-to-machine communication and other sites that simplify diagnostics of ailing machines and equipment.
The decision whether to upgrade or repair power generation plants is an ongoing process for experienced plant managers. It is important to conduct a slow investigation of your processes and throughput before you decide to upgrade or replace old equipment. Guidelines for repairing new equipment and upgrading old equipment Deciding what to do is not always easy.
When a company decides that buying new equipment is the right way to go, many decisions have to be made. Leasing new equipment may be the right choice for some companies, while others may be able to restrain their equipment for a while. Others may find that repairs or upgrading existing equipment are sufficient.
Depending on industry and type of company, a lack of new equipment can make it difficult if not impossible to accept new work or to offer new products and services as desired. New technologies and equipment make it easier for customers to think about data security New industrial equipment entices customers with higher speed and a wider range of capabilities.
It’s time to look at some serious upgrades you need to keep up with consumer demand. If your business has a product line that is growing and keeping pace, it may be the perfect time to look at industrial equipment and parts that make operations easier and increase productivity.
MACHINE VISION INTEGRATORS